Table of Contents
Timber Products introduced an automated panel repair section into their production line at their Grants Pass Plywood facility in the second quarter of 2024. The mill has been continuously operating this line with robots to patch defects on panels with the Con-Vey & Argos system ever since.
Timber Products recently started to look into an automated solution to incorporate into their panel repair line, also known as the “Patch Line.” This section of the job consisted of manually detecting defects and applying a layer of putty to create an even and smoother surface throughout the panel. Although this section of the process created good results, the production time and the labor force didn’t prove to be sufficient enough for the division’s ultimate goal.
After considering different options, the Timber Products team decided to implement the Con-Vey & Argos system, a partnership that worked to accommodate the facility’s limited space and usage. The installation was the result of three different companies coming together to make the line possible.
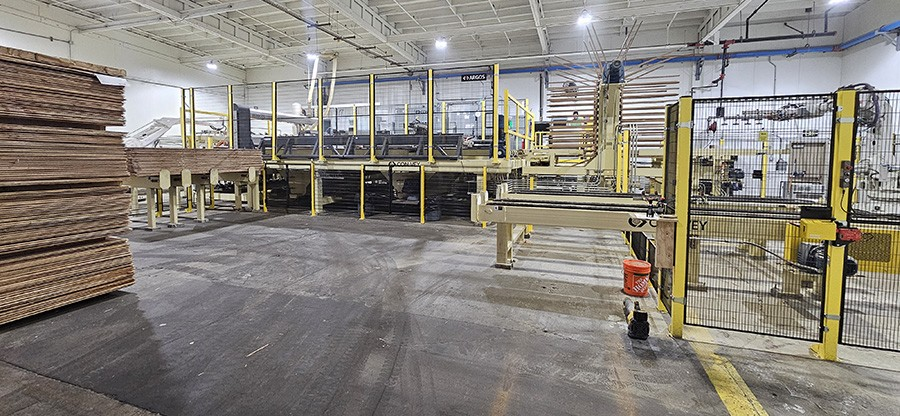
Industrial automation provider company Con-Vey installed parts of the system, including the in-feed, conveyors, vacuum table, and out-feed of the machinery, as well as seven robotic units. Other elements including the putty heads along with the router head came from Argos Solutions, a recognized Norwegian company responsible for creating automated grading and repair systems. Lastly, PRE-TEC, an automated systems integrator worked on all of the putty delivery for the patching repair.
“TP went with this particular line due to the limited amount of space Grants Pass had available and to also open the doors of robotics to the company,” explained Josh Bratton, Grants Pass plant manager.
Officials say the way the system works is truly an engineering marvel. First, a load of un-patched panels get placed on the in-feed side with the use of a forklift. The panels are then picked up by the in-feed robot that has the ability to move in four-axis directions, which then places the panel directly on the patch line. Once the panel is on the line, it goes through a scanner that determines whether the panel defects need to be routed, a poly putty application, or simply regular putty. After the correction is applied and is successfully patched, it then goes to a curing tower where the panel will be flipped by a six-axis robot.
“The out-feed robot is a six-axis robot and the reason this one is a six-axis versus the four-axis on the infeed is because we needed a way to flip panels over that did not need to be puttied on the back side,” Bratton elaborated.
The new Con-Vey & Argos Putty Repair line in the facility has proven to be successful. The former patch line required six panel patchers, which compromised other production sections due to shortage of labor force during regular operations. With the added line, only one operator is needed to patch the same amount of panels, and it will give the company an opportunity to look into patching more products in the future requiring fewer employees in mills where spots are hard to fill.
With the company introducing robotics into their facilities for automated solutions, the team is eager to see what these robots are capable of, and all of their benefits in other areas of the mill.
Visit https://timberproducts.com for more information.