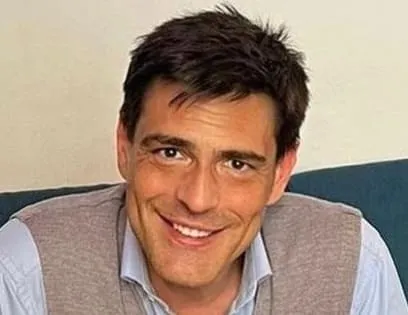
Featured
Masear to Retire after 46 Years at Black Bros.
The current Director of New Markets and Emerging Technology and Western United States Sales Representative will retire Aug. 1. Frank Bromenschenkel will take over the territory after training 18 months under the veteran.
Masear to Retire after 46 Years at Black Bros.
The current Director of New Markets and Emerging Technology and Western United States Sales Representative will retire Aug. 1. Frank Bromenschenkel will take over the territory after training 18 months under the veteran.
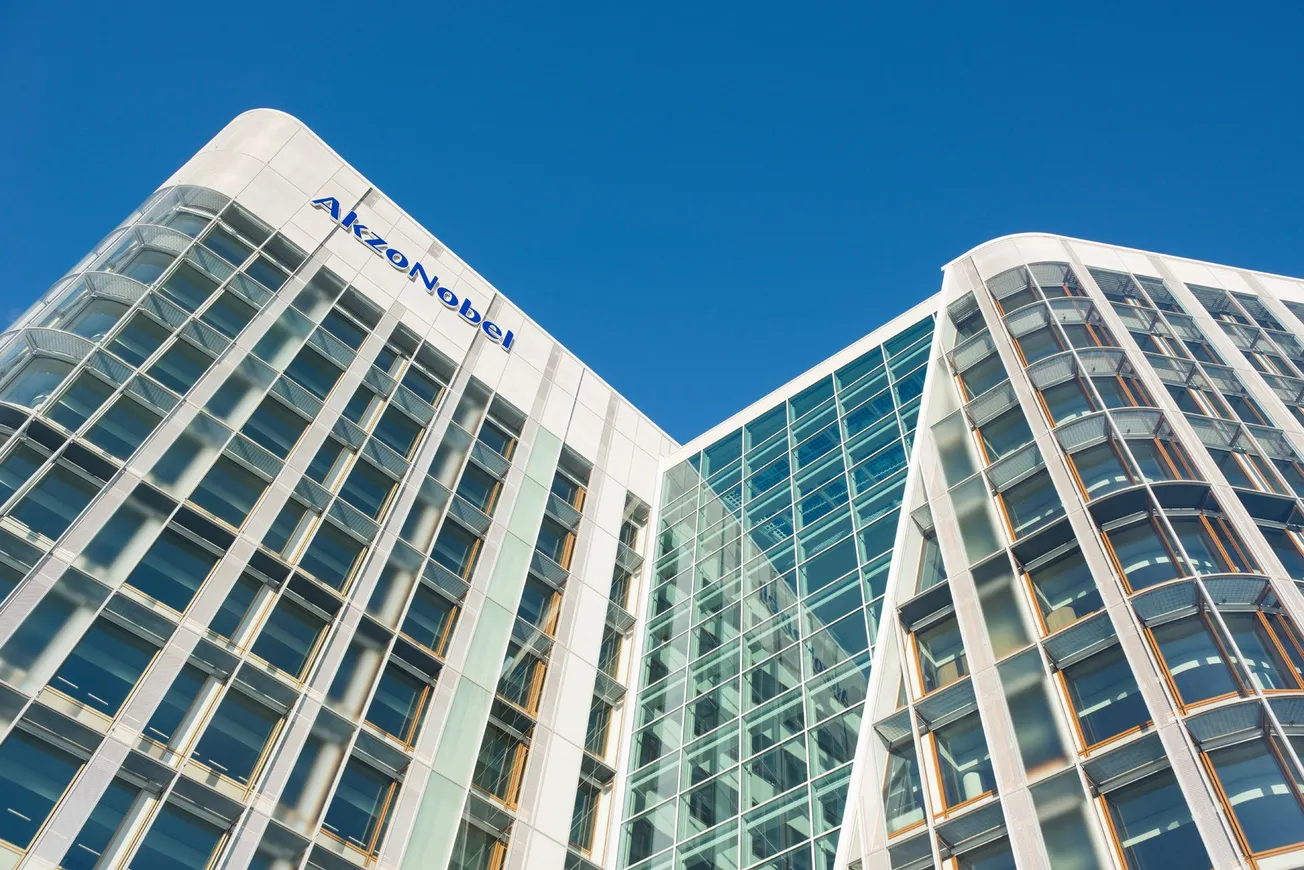
AkzoNobel to sell AkzoNobel India to JSW Group
The transaction involves the sale of up to 75 percent of shares in ANIL and is subject to customary closing conditions including regulatory approvals. The transaction is expected to be completed in the fourth quarter of 2025.
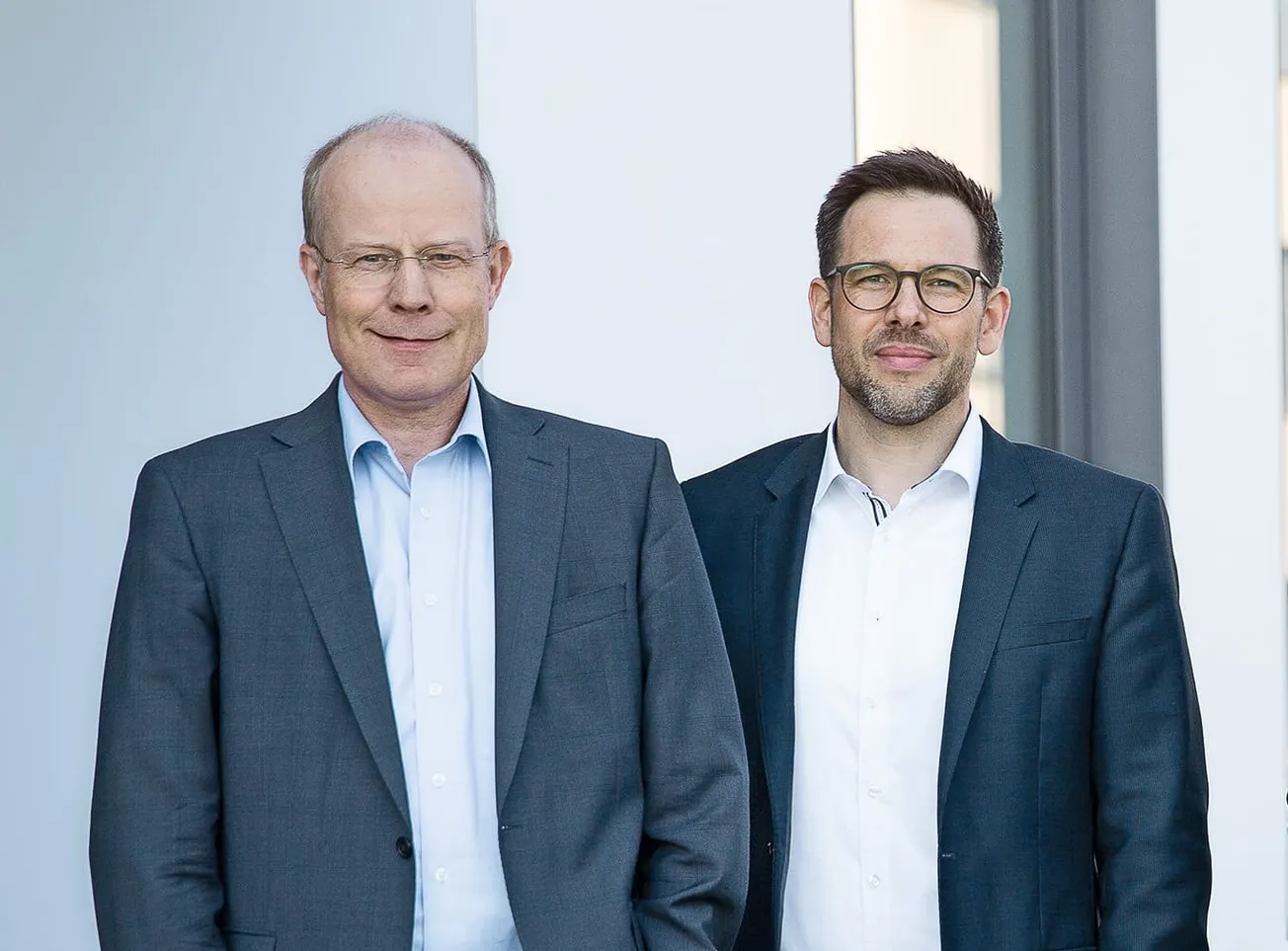
Leadership Change at the Siempelkamp Group
Dr. Stephan Niggeschmidt takes over management of the Business Unit Service from Stefan Wissing as of July 1, 2025.
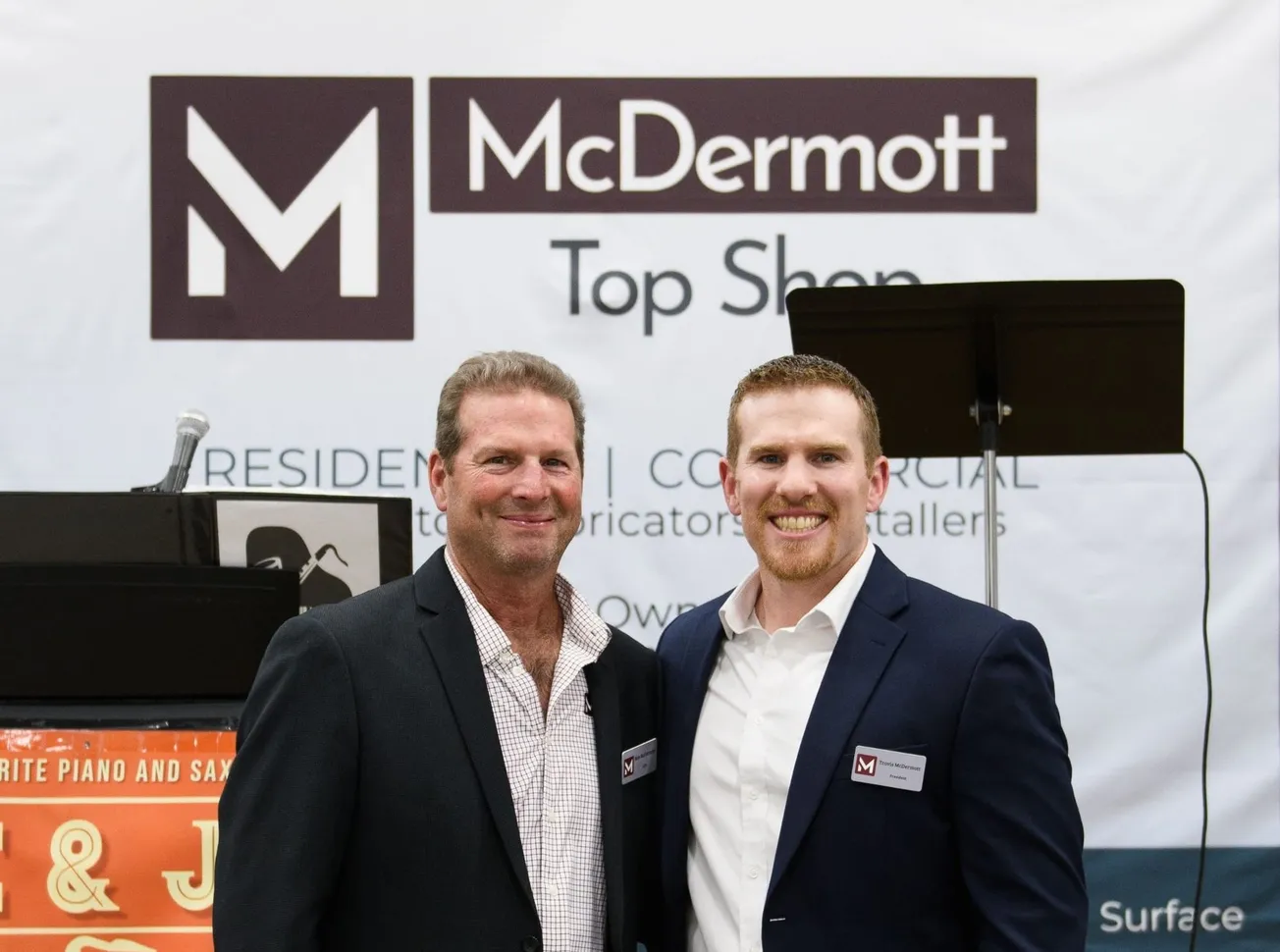
McDermott Top Shop Celebrates 30 Years of Partnership, Innovation, and Growth
The company recently celebrated its 30th anniversary with a two-part event and announced a leadership transition: Travis McDermott has been named President, with founder Ron McDermott continuing as CEO.
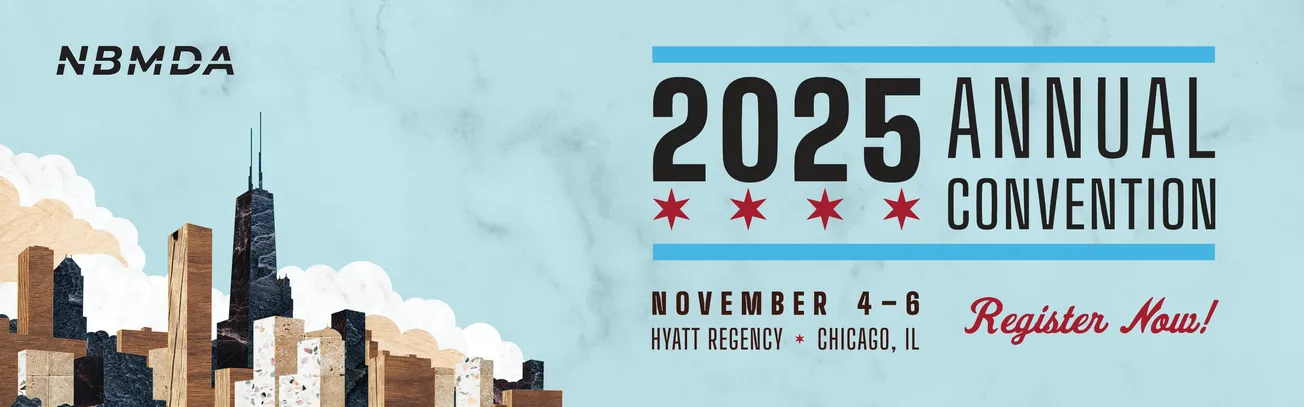
2025 NAFCD + NBMDA Annual Convention Registration Now Open
The 2025 Annual Convention will once again bring together leading distributors and suppliers from across North America’s flooring and building materials industries for three days of professional development, strategic business connection and networking.
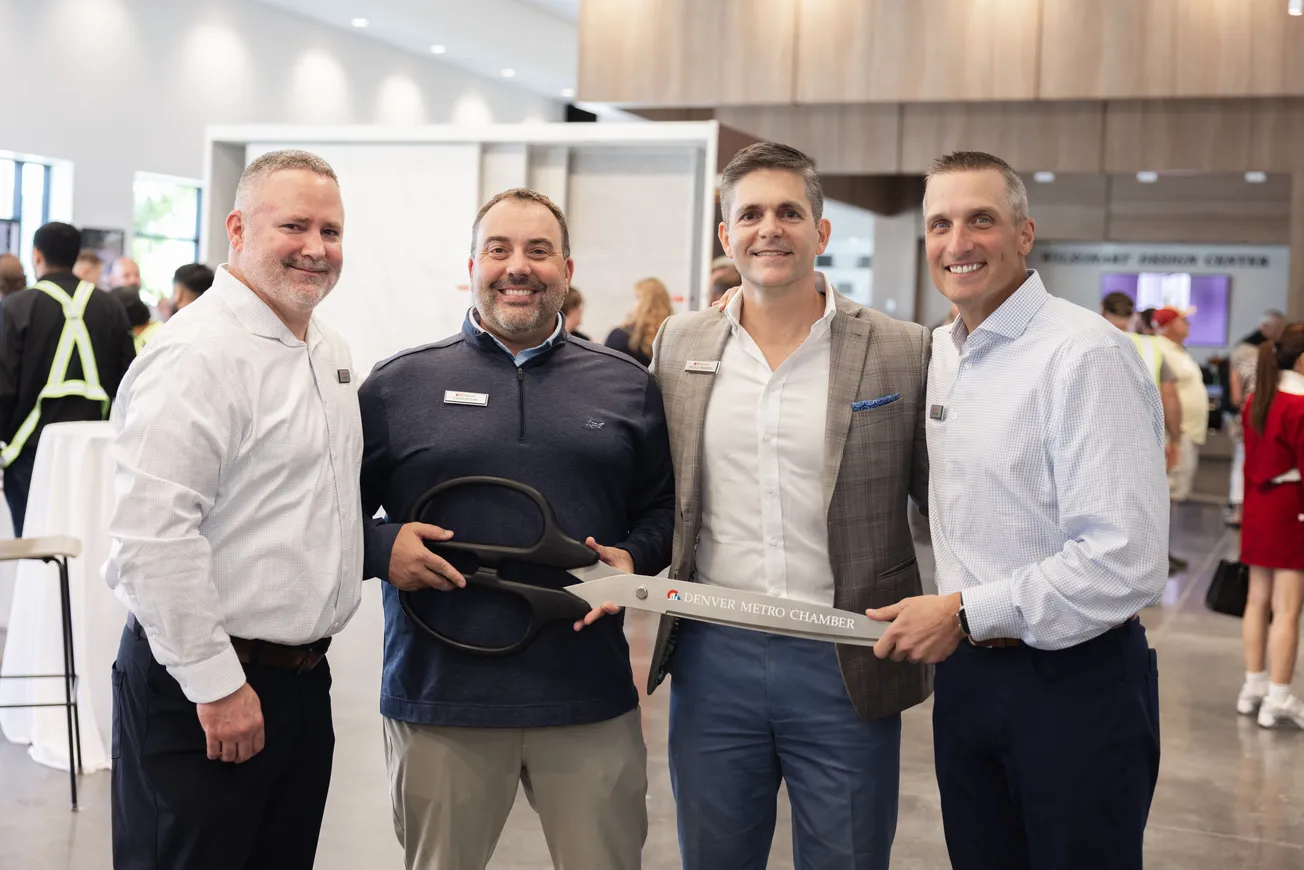
Wilsonart Opens Denver Distribution and Design Center
New 75,000-square-foot facility enhances customer experience with expanded inventory, advanced facilities and innovative design solutions
Tariffs Drive Surge in March Construction Materials Prices
National construction industry trade association Associated Builders and Contractors recently analyzed the U.S. Bureau of Labor Statistics’ Producer Price Index data released in April, finding that construction input prices continue to increase.
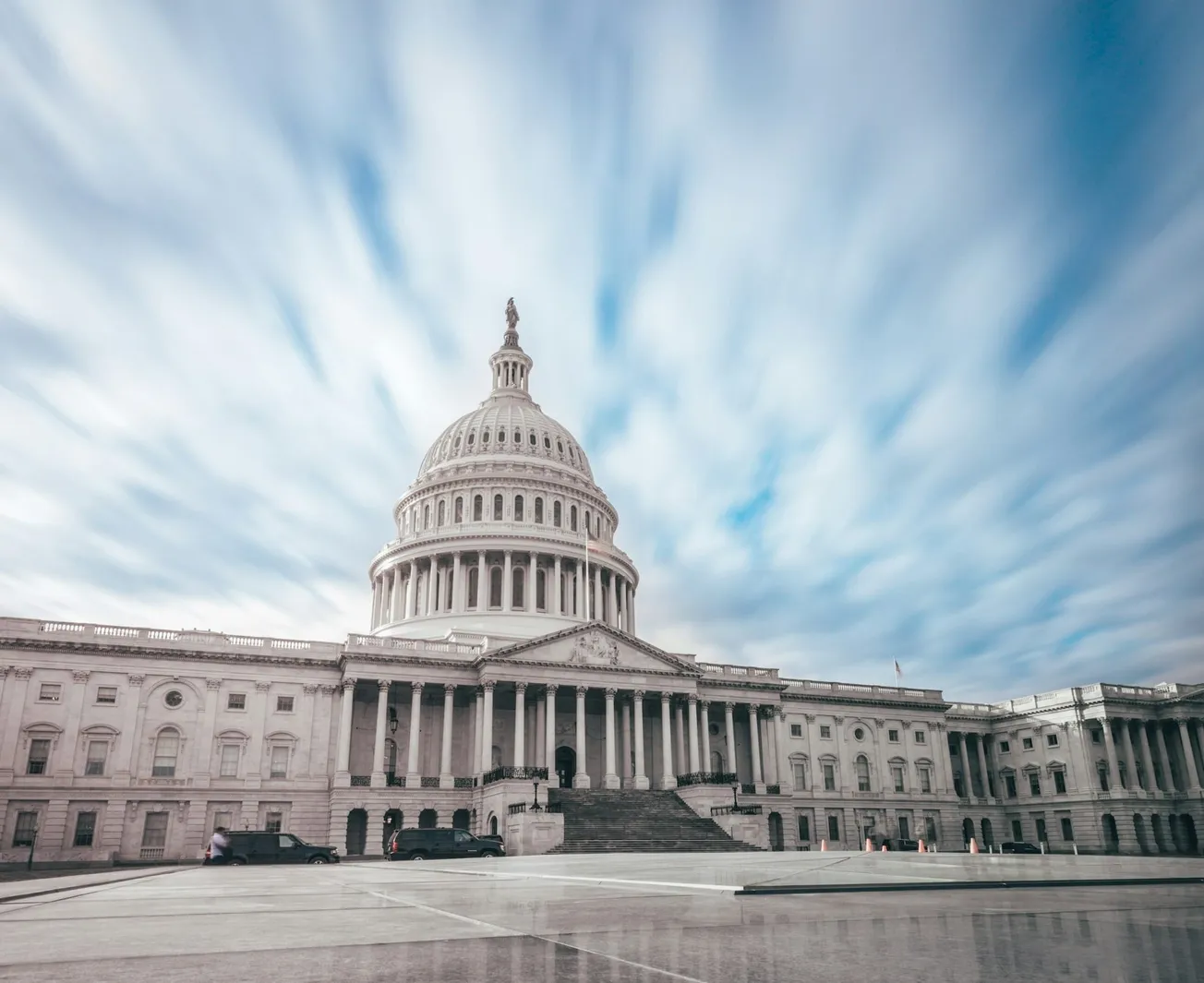
NBMDA Statement on Proposed Tariffs
The association opposes proposed new U.S. tariffs on building materials, saying they would negatively affect the nation's supply chain and building industry at a crucial time.
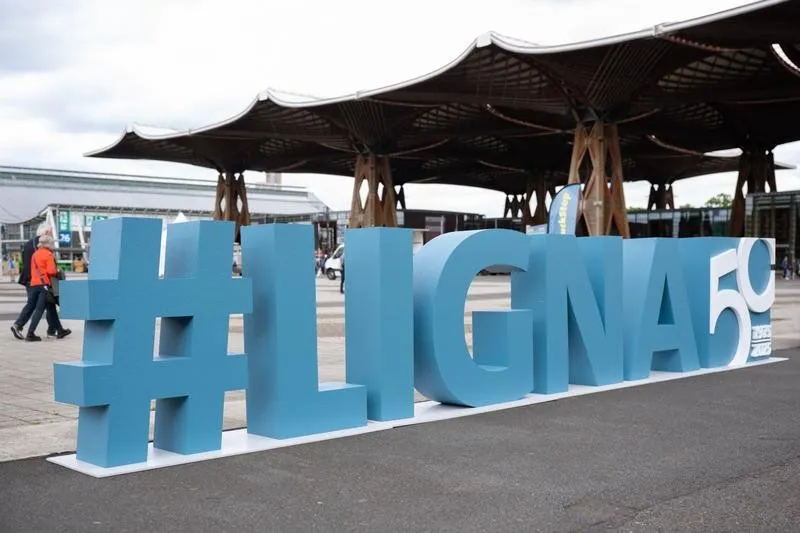
LIGNA 2025 Inspires and Motivates the Industry
In its 50th anniversary year, LIGNA 2025 once again proved to be the leading platform for the international woodworking community, featuring 1,433 exhibitors from 49 countries.
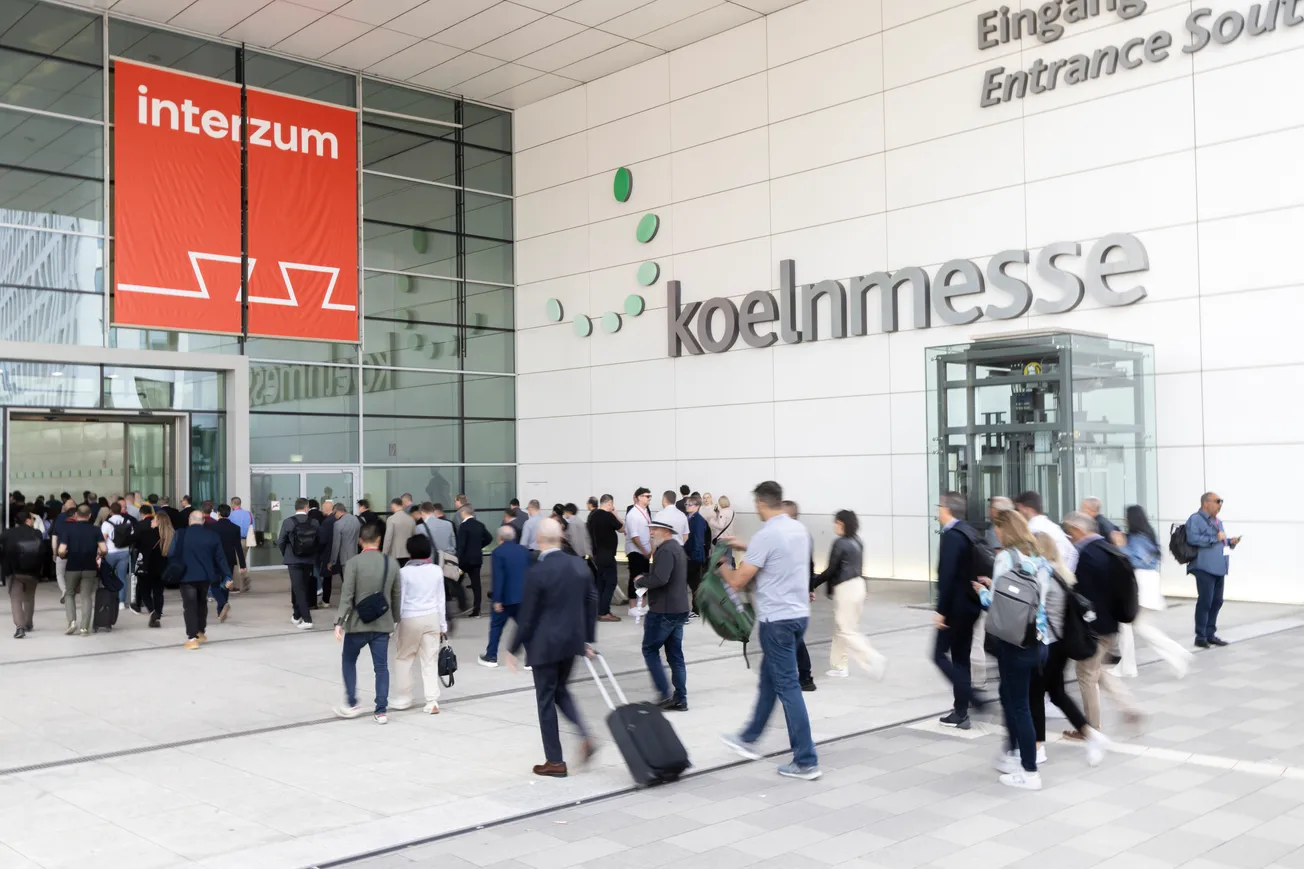
interzum 2025: Setting a Course for the Future
For four days, Cologne became the international stage for innovative materials, intelligent components and smart technologies that will shape the homes and workplaces of tomorrow, with around 60,000 trade visitors from 148 countries and over 1,600 exhibitors from 57 countries.
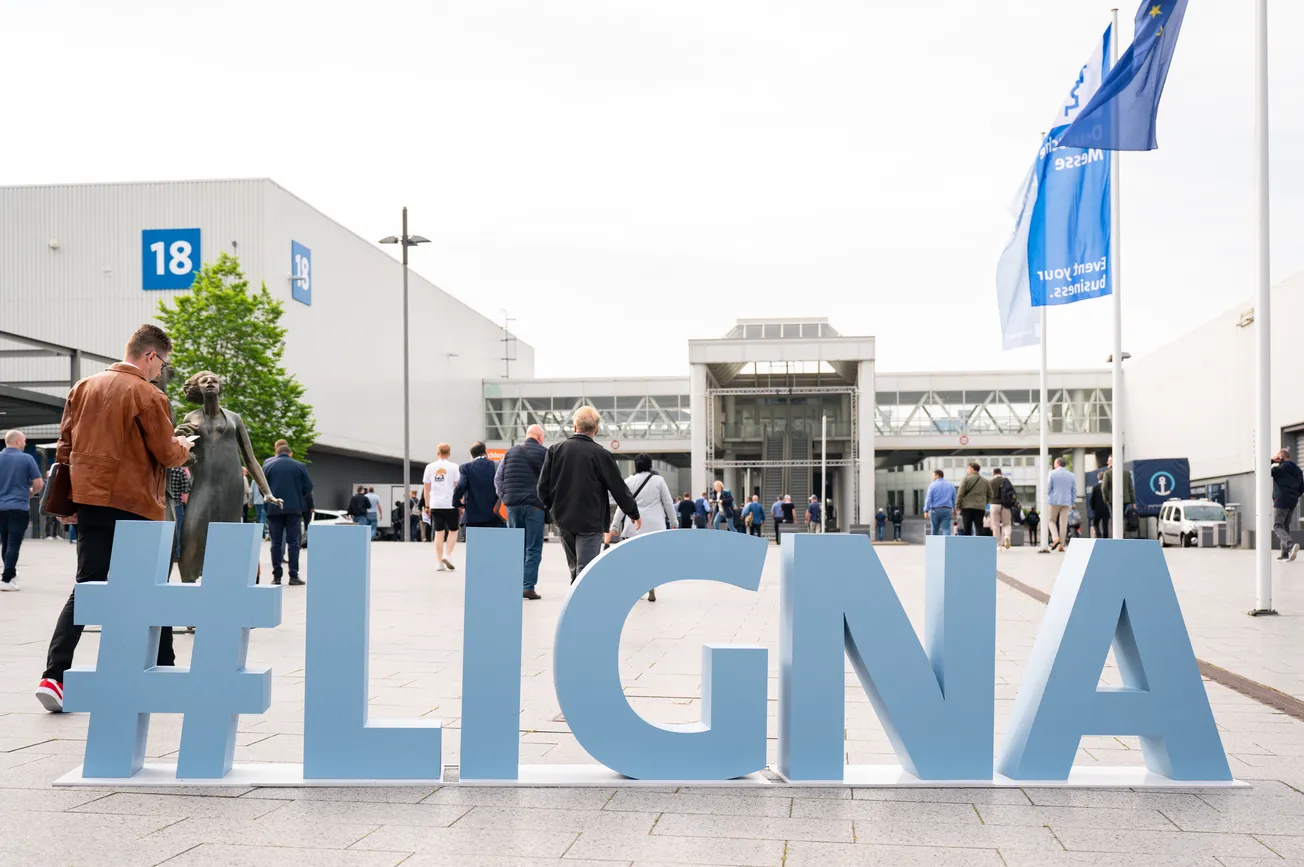
LIGNA 2025 to Spotlight Vital Forests
The forestry section of the 50th anniversary of LIGNA 2025 will showcase all aspects of optimized timber harvesting methods, reflecting the importance of wood as a raw material to the global woodworking and wood processing industry.
Tariffs Drive Surge in March Construction Materials Prices
National construction industry trade association Associated Builders and Contractors recently analyzed the U.S. Bureau of Labor Statistics’ Producer Price Index data released in April, finding that construction input prices continue to increase.
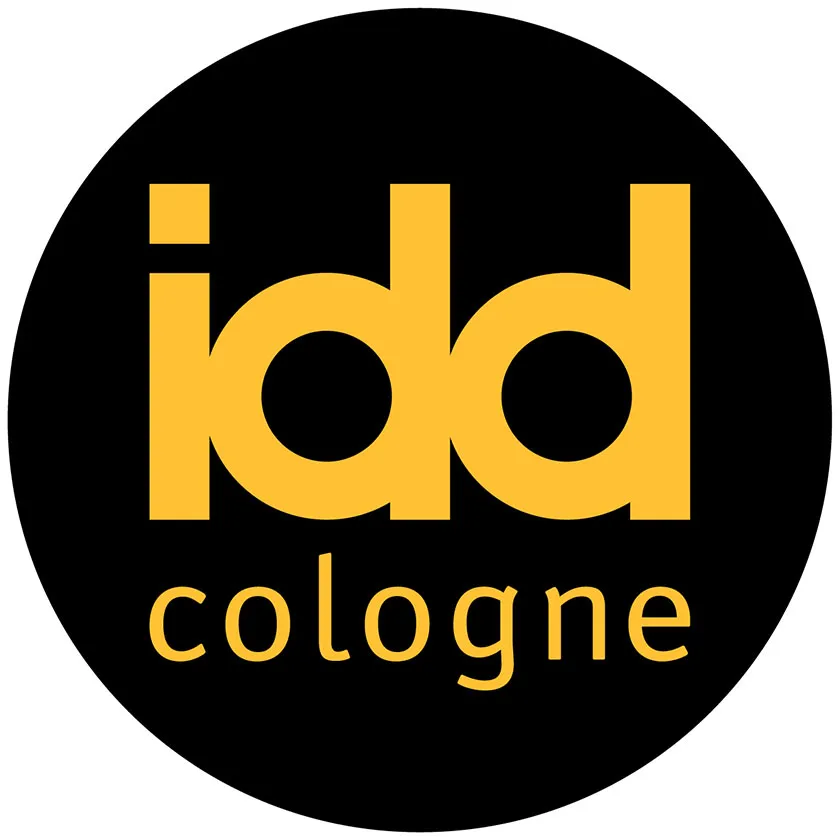
New Trade Fair Launches This Fall in Cologne
Featuring inspiring design and an innovative concept, “idd cologne” and “idd cologne downtown” will bring interior design to Cologne’s city center October 26-29.
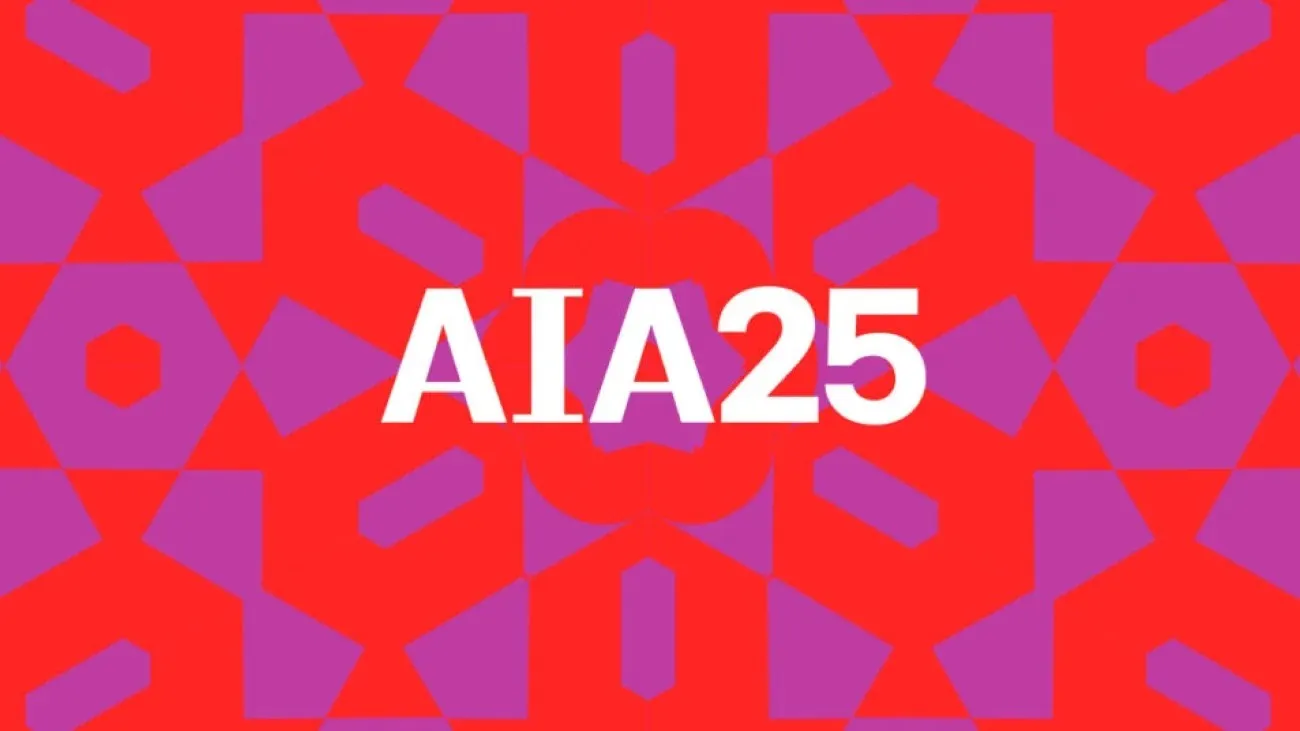
AIA Elects New Leaders
Three new leaders were elected during the recent AIA25 annual conference in Boston.
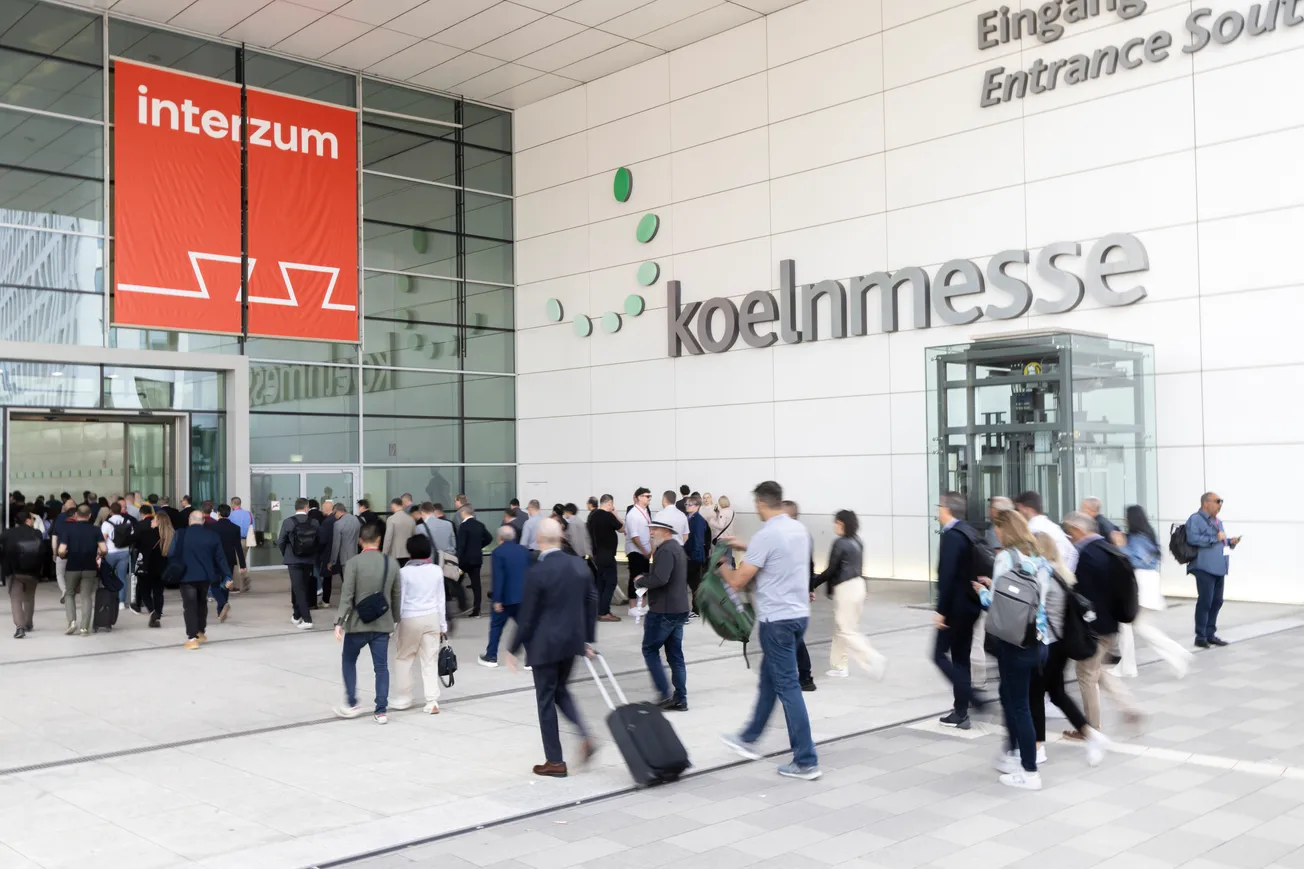
interzum 2025: Setting a Course for the Future
For four days, Cologne became the international stage for innovative materials, intelligent components and smart technologies that will shape the homes and workplaces of tomorrow, with around 60,000 trade visitors from 148 countries and over 1,600 exhibitors from 57 countries.
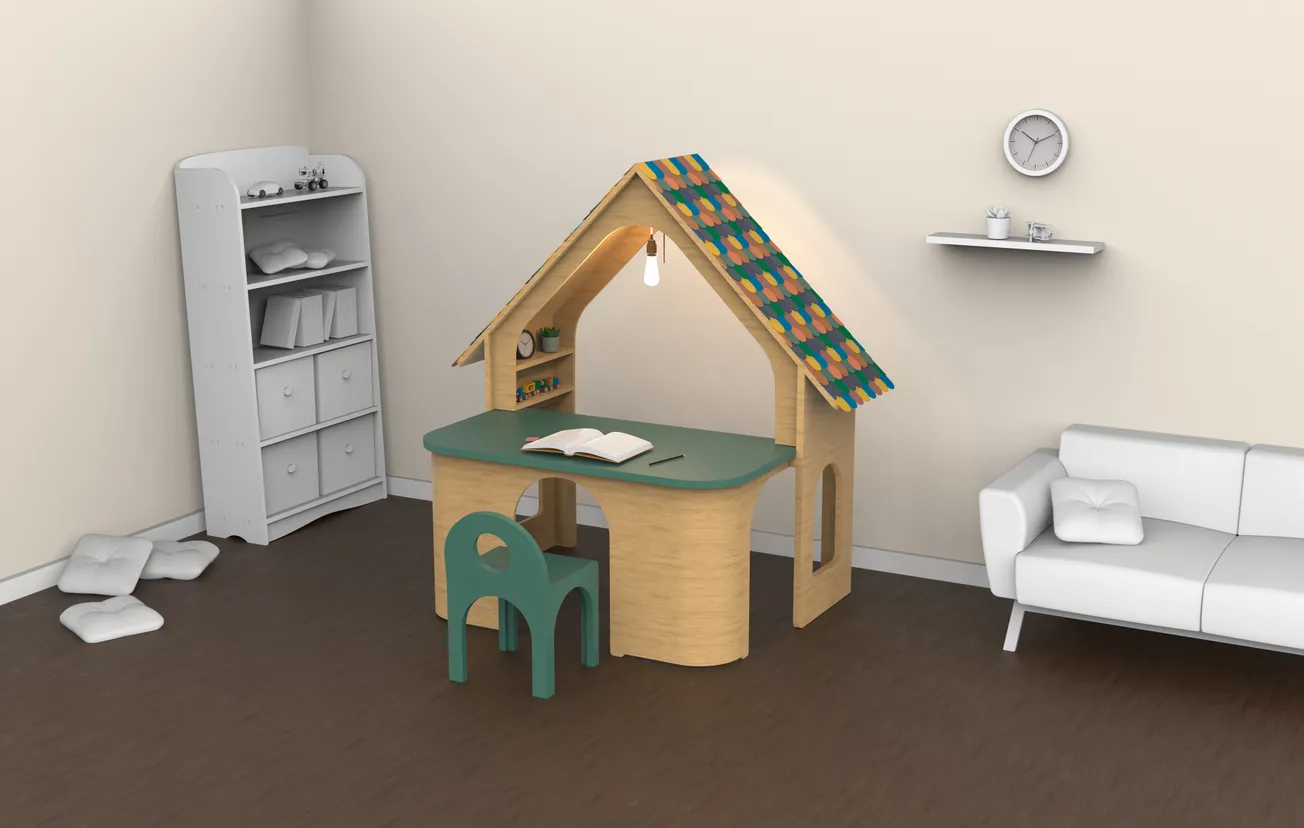
FORM Student Innovation Competition Winners Announced
Nearly 200 eligible submissions were considered for Formica’s eighth annual student design competition, which challenged students to create furniture pieces utilizing Formica Brand products that aligned with this year’s theme of “Designing for Wellbeing.”
Editors' Picks
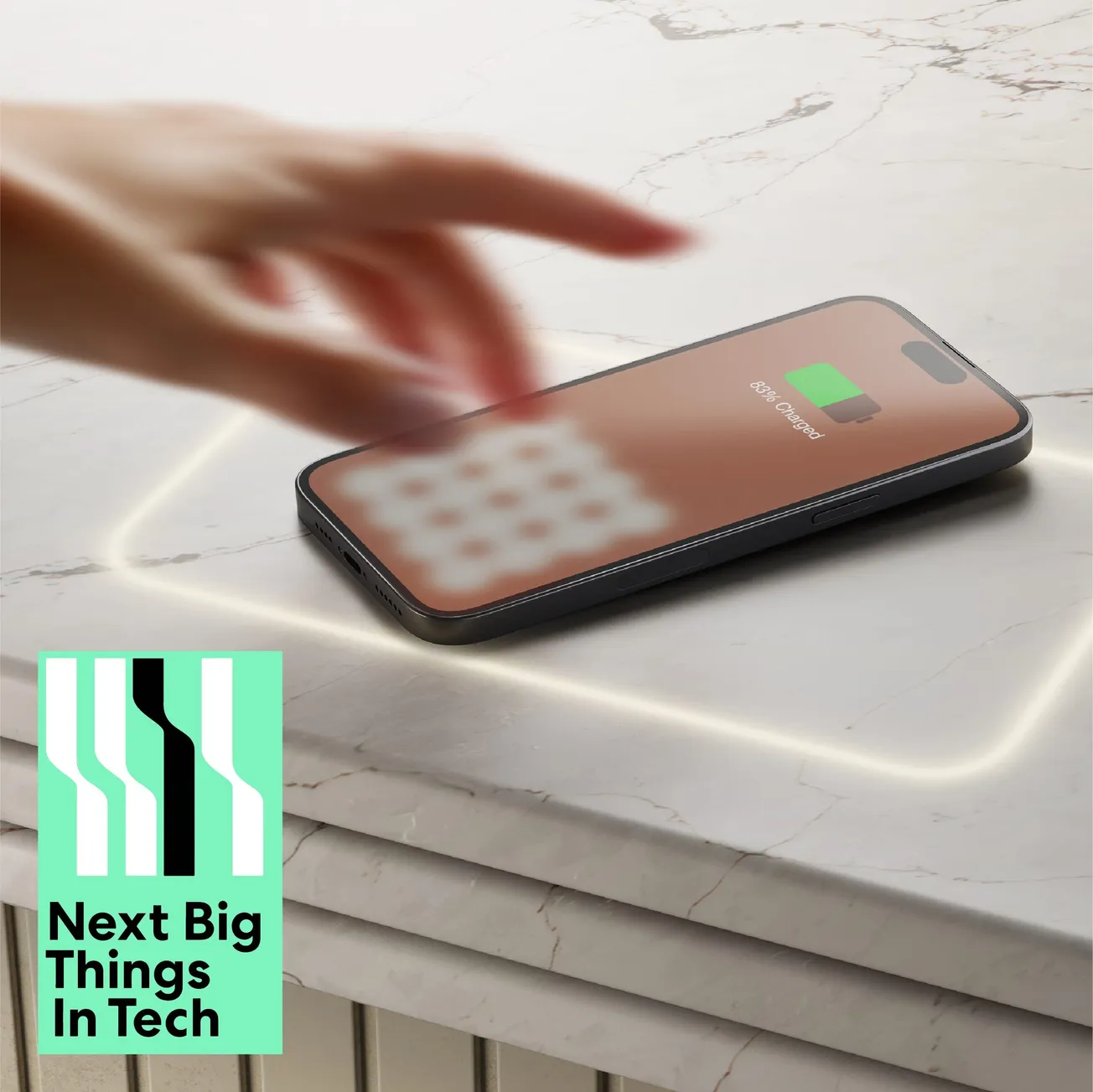
FreePower Named “Next Big Things in Tech”
The award from Fast Company recognizes breakthrough innovations that are poised to transform everyday spaces, gadgets, wellness, and more.
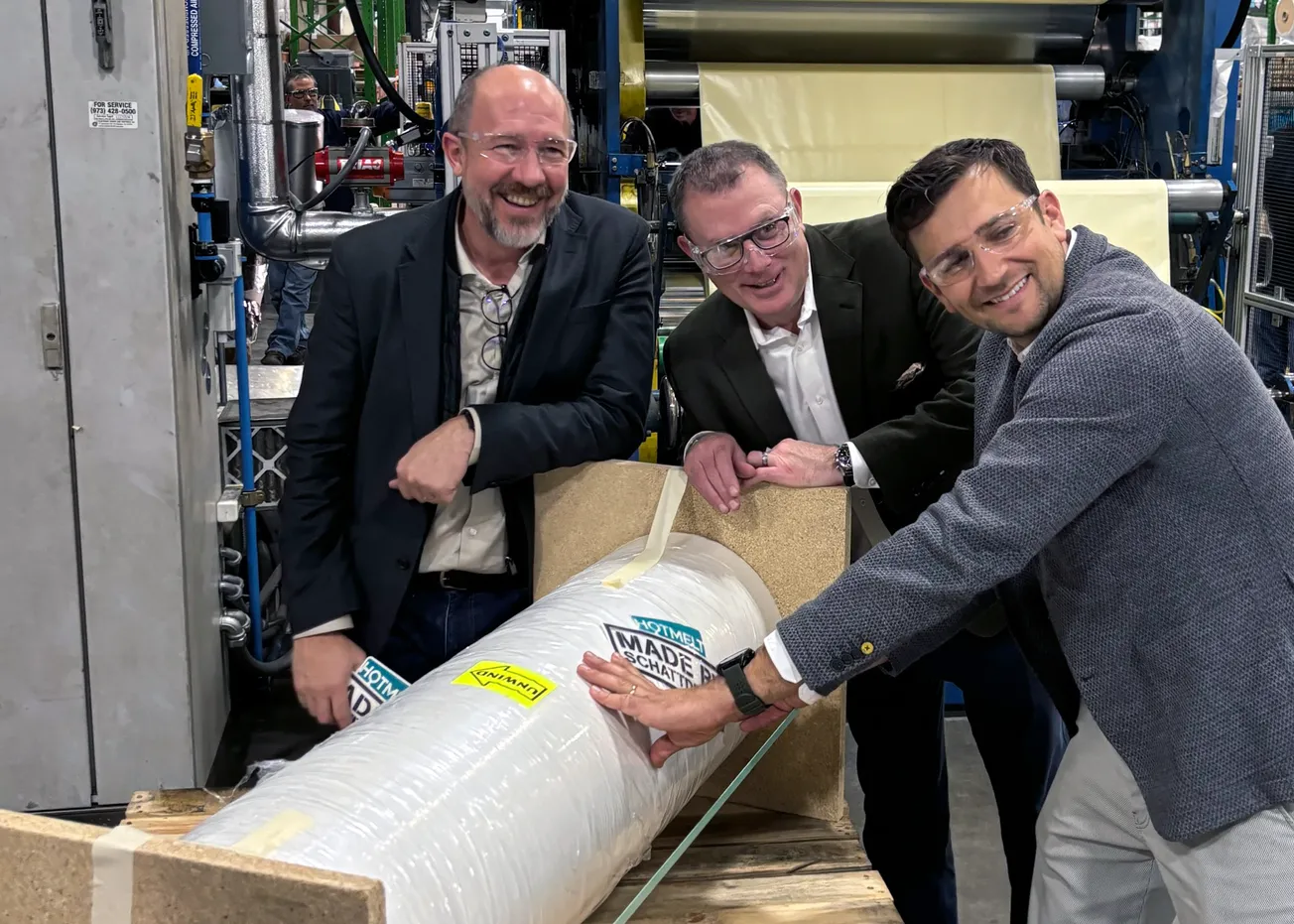
Schattdecor Starts Up Hotmelt Adhesive Production in Lexington
The new production line significantly enhances the company's ability to serve its customers, offering a complete solution from a single source.
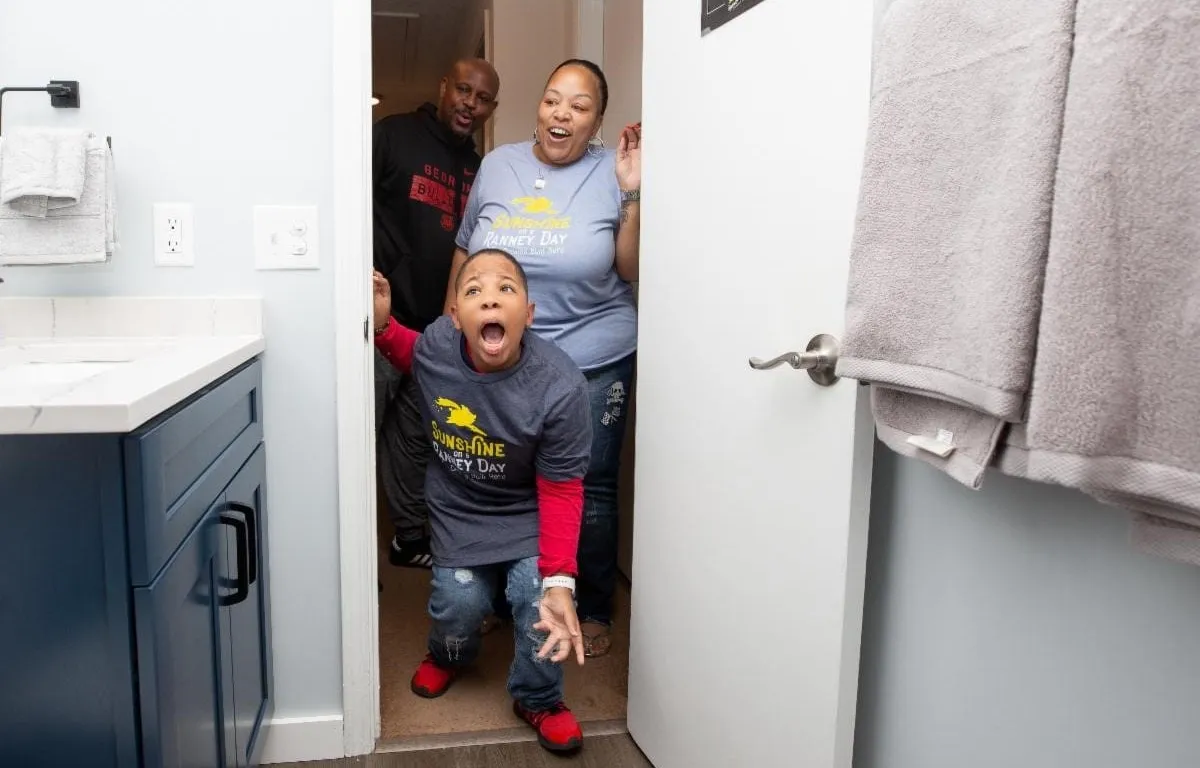
Accessible Spaces for Kids Reimagined Through Partnership
Hardware manufacturer Top Knob has partnered with nonprofit Sunshine on a Ranney Day to create inclusive spaces for children with special needs.
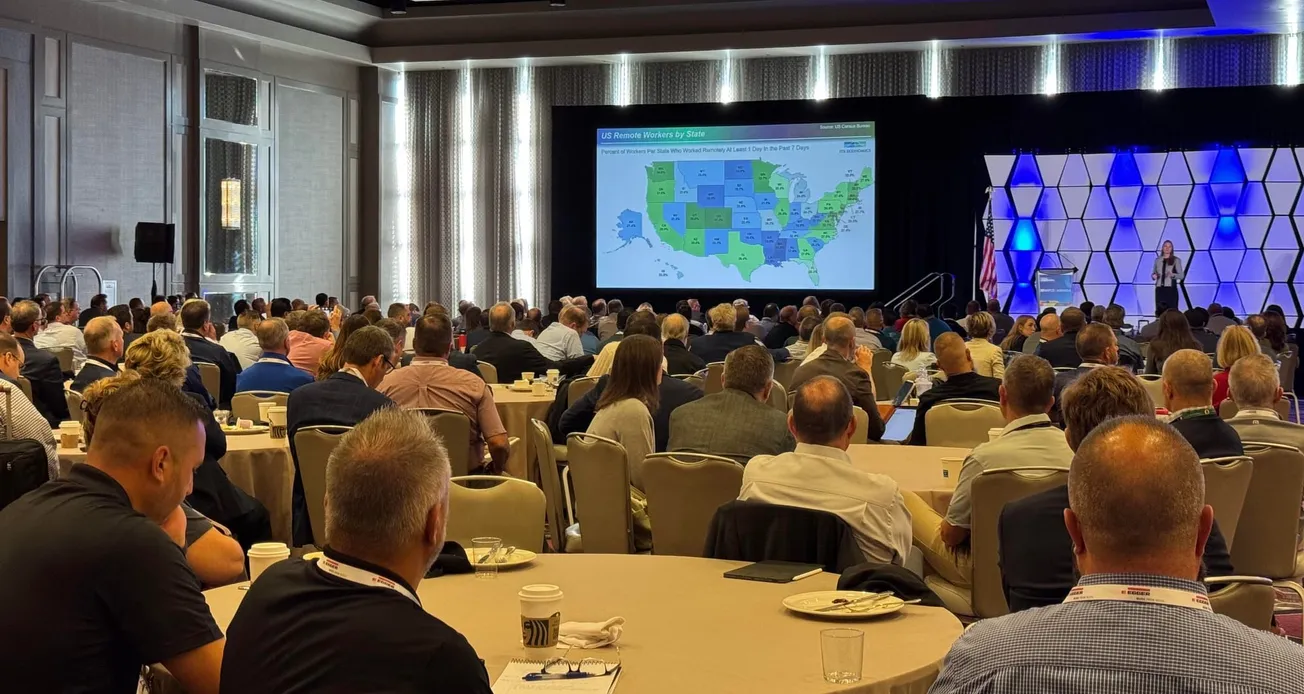
Historic 2024 NAFCD + NBMDA Convention Makes its Mark
The recent 2024 NAFCD + NBMDA Annual Convention in New Orleans proved to be a great success, with engaging and informative speakers and a full show floor. Officials say it was one of the largest events in the history of the convention.